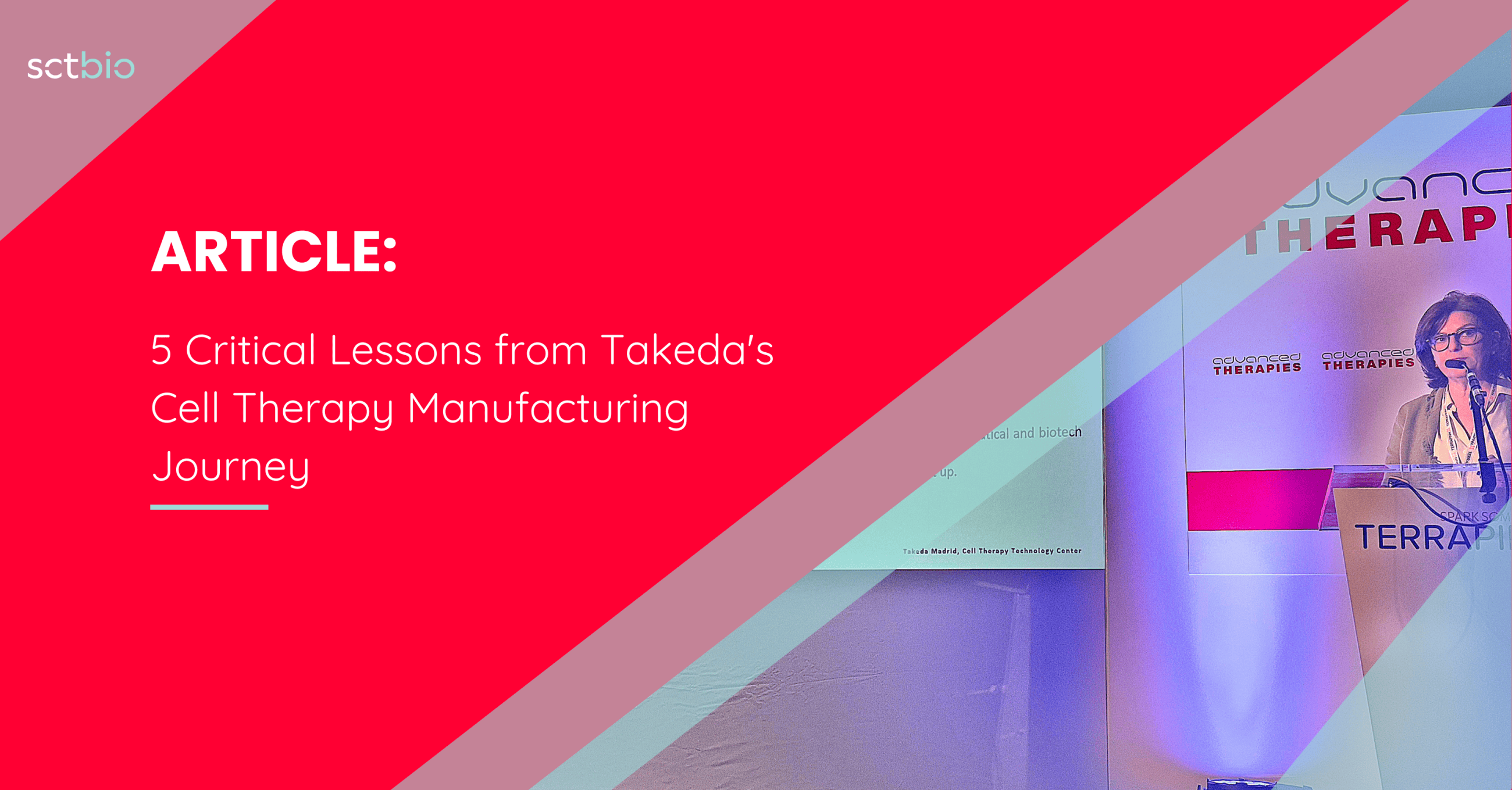
5 Critical Lessons from Takeda's Cell Therapy Manufacturing Journey
Last week at Terrapinn's Advanced Therapies UK event, Pilar Redondo, Site Head of Takeda's Madrid facility, share invaluable insights from her and her team’s pioneering work in cell therapy manufacturing. As the facility behind Alofisel, the first allogeneic cell therapy approved in the European Union, their journey offers a treasure trove of lessons for anyone in the cell and gene therapy space.
Though the therapy was ultimately withdrawn from the market in December 2024, the legacy of innovation and excellence cultivated at the Madrid facility continues to set a shining example for cell therapy manufacturing.
Here are the five most critical lessons from Takeda's experience:
1. The Control Strategy Paradox: Narrower Isn't Always Better
Perhaps the most striking insight was how the approach to control strategies evolved over time. Initially, with limited manufacturing experience, the team established narrow specification limits believing tighter control would ensure quality. What they discovered instead was that overly restrictive parameters created unnecessary operational problems.
"What you find along the way is many issues, many problems that were probably avoidable by defining the control strategy a bit better..."
Key takeaway: When developing control strategies, resist the temptation to set unnecessarily tight specifications. Instead:
- Gather extensive data from the earliest possible stage
- Establish continuous re-evaluation as part of your lifecycle management
- Consider CQAs, process parameters, and materials holistically
- Begin data compilation much earlier than you think necessary
2. Digital Transformation Creates Visibility That Drives Excellence
What stood out in Takeda's approach was how they transformed a legacy manual process through strategic digitalization. Rather than digitizing for its own sake, they focused on creating visibility that could drive decision-making.
Their comprehensive digital infrastructure – from ERP systems to electronic batch records and environmental monitoring – generated data that fuelled continuous improvement. KPIs evolved from basic metrics to sophisticated governance tools. Process monitoring matured into continuous verification directly tied to control strategy.
Key takeaway: Digital transformation should be approached as an enabler of visibility and process understanding, not just modernization:
- Implement compliant systems that generate actionable data
- Use digital tools to create KPIs that drive governance
- Apply data science principles to evaluate control strategies
- Let data guide your continuous improvement efforts
3. Planning for Commercial Scale Must Start in R&D
One of the most candid admissions was how the manufacturing process, defined early in clinical development, created limitations when scaling for commercial demand. Without a clear scale-up strategy, they team found themselves "essentially scaling out rather than scaling up," making efficiency improvements difficult and increasing variability risks.
Key takeaway: Build commercial manufacturing considerations into your earliest process development:
- Implement a formal lifecycle management strategy from day one
- Define specific stages for process review throughout development
- Develop robust comparability protocols to support process evolution
- Consider how your process will scale before you're forced to scale it
4. Cross-Functional Integration Powers Innovation
What made Takeda's Madrid site unique was its co-location of GMP manufacturing alongside R&D functions. This structural choice created a rich environment where manufacturing sciences, analytical sciences, and technology teams could collaborate seamlessly. These teams became instrumental in troubleshooting methods, supporting investigations, and driving continuous improvement.
Key takeaway: Break down traditional silos between R&D and manufacturing:
- Co-locate teams when possible
- Create formal connections between R&D and GMP operations
- Ensure technical teams participate in deviation investigations
- Let scientific understanding drive operational excellence
5. Regulatory Engagement Should Be Continuous, Not Episodic
Throughout her presentation, Pilar emphasized that continuous engagement with health authorities was "absolutely a must" for navigating the regulatory landscape. Rather than treating regulatory interactions as discrete events, Takeda's approach involved ongoing dialogue from early development through post-commercialization.
Key takeaway: Develop a continuous regulatory engagement strategy:
- Begin dialogue early in development
- Share development challenges transparently
- Seek scientific advice at critical process change points
- Build relationships that facilitate ongoing communication
The Ultimate Learning: People Make the Difference
While technical and digital transformations were crucial, the presentation concluded with emphatic emphasis on what was described as the secret ingredient in the sauce.
The people.
Takeda’s Madrid site benefited from diverse talent with complementary expertise across multiple disciplines.
"The secret ingredient to make any project successful is to have the right team, to have the right talent,"
Despite the ultimate withdrawal of Alofisel from the market in December 2024, the learnings from Takeda's Madrid facility represent an enduring contribution to advancing cell therapy manufacturing. Their journey reminds us that success in this field requires not just scientific innovation but operational excellence, digital transformation, and most importantly, the right team with the right mindset.